IWC Schaffhausen has proudly unveiled its groundbreaking innovation, the patented Ceralume technology. This unique process, developed by IWC’s XPL experimental engineering department, has led to the creation of the world’s first fully luminous ceramic watch case. The technology involves a meticulous blend of ceramic powder and high-quality Super-LumiNova luminous coating pigments, a material that stores light energy. In rigorous darkroom tests, the Ceralume luminous porcelain technology demonstrated its endurance, emitting a vibrant blue light for over 24 hours.

Ceramic, known for its lightweight, extreme hardness, and high scratch resistance, has been a critical focus for IWC since 1986 when it introduced the world’s first watch with a black zirconium oxide ceramic case. The brand’s ceramic innovations have continued with brown silicon nitride ceramic cases and black boron carbide ceramic cases, one of the most complex substances known. Following the success of the TOP GUN ceramic watches, IWC is now pushing boundaries with the Ceralume technology, a luminous ceramic material produced using a patent-pending, highly engineered manufacturing process.
“With the first fully luminous ceramic case bezel, we are underscoring our role as a pioneer and innovator in ceramic replica watches. The development of Ceralume took several years. The main challenge was to produce a case with extremely high grain uniformity and meet our stringent quality standards,” explains Dr. Lorenz Brunner, Head of Research and Innovation at IWC Schaffhausen.
This eye-catching luminous effect is achieved by mixing high-quality Super-LumiNova luminous coating pigments into the ceramic raw material. Produced by Swiss technology company RC Tritec, Super-LumiNova is a high-tech ceramic compound that behaves like a photovoltaic cell. The material absorbs light energy from sunlight or artificial light and stores it temporarily before emitting it again as visible light. This cycle can be repeated unlimited times without causing the material to age or reducing its light storage capacity. The Ceralume case glowed bright blue in darkroom tests for more than 24 hours. Fake watches for sale.
A highly engineered process makes Ceralume technology.
Conventional white ceramics are made by mixing zirconium oxide with other metal oxides. These powders are shaped into so-called “blanks,” machined to a geometry close to that of the final case, and then sintered in an oven at high temperatures. Super-LumiNova luminous coating pigments are added to the raw material mix to make the white ceramic glow in the dark. One of the main challenges in developing Ceralume technology was to achieve the most uniform mixing possible despite the different particle sizes of the raw materials to avoid particle accumulation. To achieve this, IWC engineers reverted to a dedicated ball milling process that had to be tailored to the raw materials used. In addition, the sintering process and the grinding parameters of the sintered ceramic body also needed to be specifically adapted to the needs of luminous ceramics.
The first all-luminous ceramic concept watch
IWC’s XPL experimental engineering department uses the new Ceralume luminous ceramic technology to create a fully luminous ceramic concept watch for the first time. In addition to the Ceralume luminous ceramic case, this concept watch, based on the Pilot’s Watch Chronograph 41 design features, is also equipped with a white luminous dial and a white luminous rubber strap. The dial and strap are coated with Super-LumiNova luminous coating. The brass base of the dial is sprayed with Super-LumiNova solution and then printed on the luminous coating. The white rubber strap is made of injection molding and has Super-LumiNova luminous coating pigments.
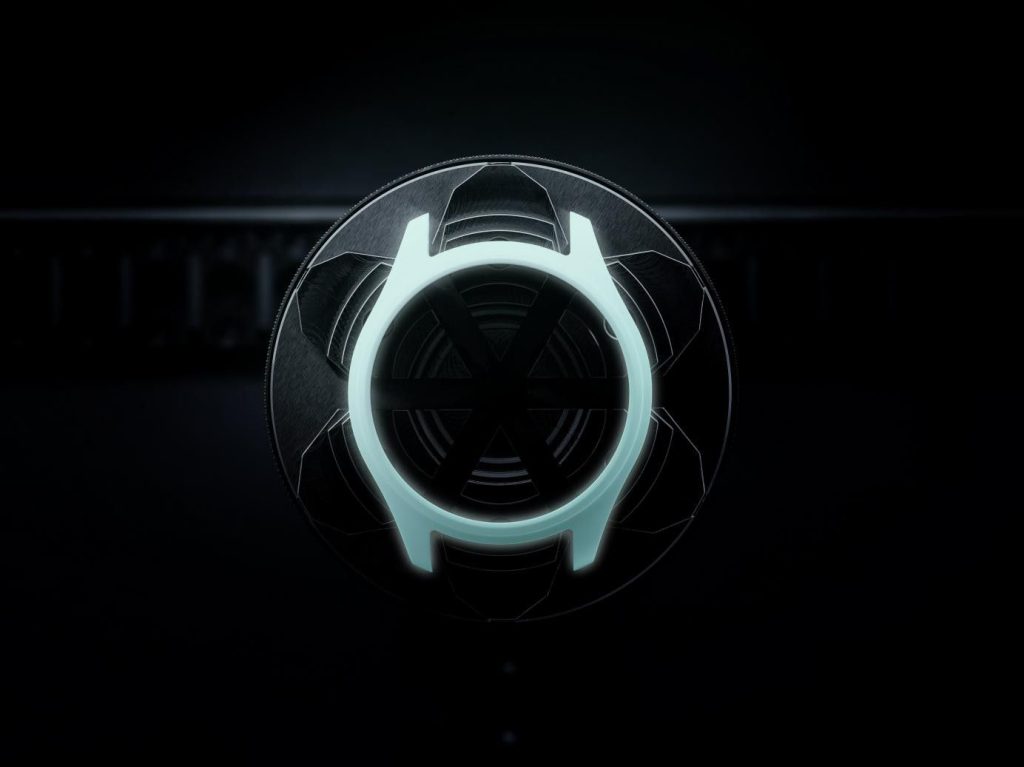
The Ceralume luminous ceramic technology developed by IWC Schaffhausen is patented and will become the basic technology for watch development and new releases.